Voilà deux ans à peu près que j’ai bricolé un « fil chaud », un de ces outils électriques destinés à découper (principalement) le polystyrène pour réaliser les décors de nos chers jeux.
Même si je ne m’en sers pour ainsi dire jamais, c’est un projet sur lequel j’ai pris beaucoup de plaisir et je ne doute pas qu’il saura en inspirer quelques-uns parmi les lecteurs de ce blog.
Vous trouverez quelques liens commerciaux au long de cet article, ils sont présent uniquement pour donner un exemple des équipements dont il est sujet, ç titre informatif. Il ne s’agit en aucun cas de liens affiliés. 🙂
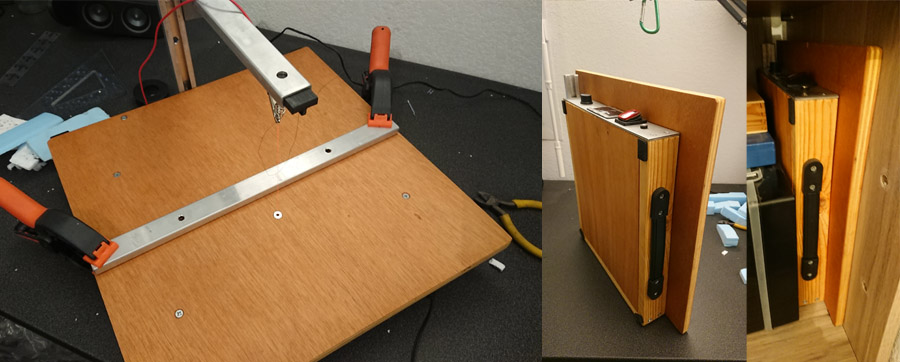
Le fil chaud, présentation et principe de fonctionnement (dans les grandes lignes).
Pas mal d’entre vous connaissent sûrement déjà la bête, mais je fais tout de même une piqure de rappel.
On nomme « fil chaud » (ou « hot wire ») un dispositif faisant passer un courant électrique dans un fil métallique, ce qui a pour effet de le faire monter en température et permet à terme de s’en servir pour découper facilement et proprement les matériaux sensibles à la chaleur, tels que certains plastiques et acryliques, mais surtout le polystyrène et différentes mousses expansées, ce qui justement nous intéresse dans cet article.
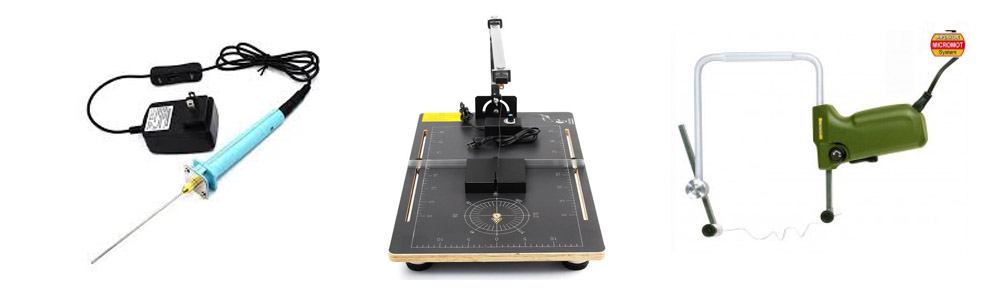
Certains métaux sont particulièrement efficaces dans cette utilisation, tels que le nichrome que nous allons justement utiliser.
Plus le courant est fort et plus le fil de métal est court, plus la chaleur dégagée sera importante. Sur les modèles fais maison il est donc courant de devoir jouer simultanément avec l’intensité du courant et la longueur du fil pour régler au mieux la température.
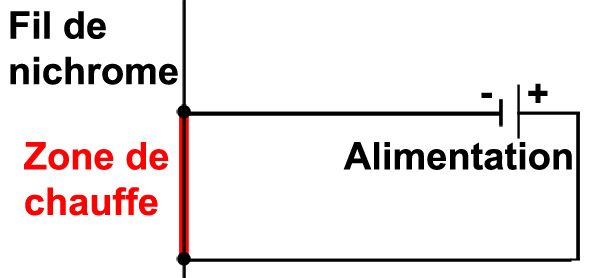
Don’t try this sh*t at home…
…ou du moins pas avant d’être conscient des risques liés à son utilisation.
On parle ici de métal chauffé parfois jusqu’au rouge, donc littéralement de métal proche de la fusion. Donc ça brûle. Fort.
Vous l’aurez compris, une fois la bête allumée, on ne touche pas le fil, ni même tout de suite après utilisation, il refroidit assez vite, mais tout de même.
Il est important aussi de ne pas trop faire chauffer le fil, s’il tire trop longtemps au rouge il cassera et pourrait créer des projections de matière.
L’autre danger, plus pernicieux, ce sont les vapeurs. On brûle ici des matières plastiques et les vapeurs qui s’en dégagent sont tout sauf saines, les volutes de fumée et l’odeur vous en convaincront. Il est donc impératif de pratiquer dans un endroit ventilé, à l’extérieur de préférence, ou au moins devant une fenêtre. Si vous ajoutez à cela un masque, ce n’est que mieux.
Et bien sûr en faire une utilisation responsable, ce qui implique par exemple de ne pas avoir d’enfants à portée, de ne pas la laisser allumée si vous n’êtes pas à côté, ou encore de ne pas essayer de découper n’importe-quoi avec (on évitera par exemple le papier).
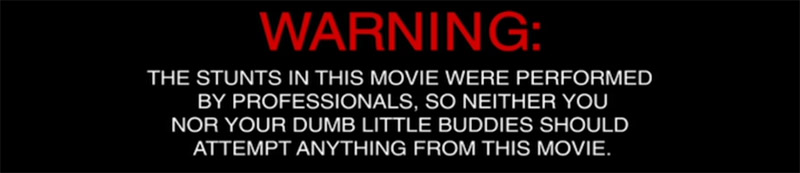
Cahier des charges
La première chose qu’il m’a fallut faire, c’est mettre à plat les attentes que j’avais vis à vis du produit fini. Je voulais qu’il soit :
- Petit budget
- Polyvalent
- Capable de couper des morceaux d’une hauteur d’environ 10cm
- Relativement solide
- Facile à régler
- Facile à mettre en place
- Facile à ranger
- Facile à transporter
Après quelques réflexions, je suis parti sur ce qui me paraissait le plus simple : l’ensemble serait démontable et tout se rangerait dans un coffret bois qui ferait aussi office de surface de travail. Le coffret devrait être assez haut pour contenir tout le nécessaire mais aussi assez petit pour ranger l’ensemble dans un placard tel un livre et la surface de travail devait être assez grande pour travailler à l’aise mais pas trop grande pour éviter que le rangement ne soit un problème.
La liste de courses
L’air de rien, il me fallait pas mal de matos pour réaliser la bête :
- Du bois pour le coffret : j’ai utilisé des chutes de bois qu’on trouve à prix réduit dans les magasins de bricolage, à 0.50€ ou 1€ le carré de 40x40cm, c’était parfait .
- Pour la potence qui tient le fil chaud, j’ai utilisé du profilé en aluminium trouvé dans les chutes à mon travail.
- Pour l’électronique, après avoir fait le tour de mon petit stock j’ai acheté le reste chez nos grossistes chinois que nous connaissons si bien. Il m’a fallut un transformateur 12 ou 24V, de quoi le raccorder, un interrupteur, un potentiomètre, des pinces crocodiles, du fil électrique, le fil de nichrome et enfin de la gaine thermique (pour faire les choses bien).
En fouillant dans mon bazar, j’ai trouvé un transformateur 12V à 2A, parfait pour moi. 2 ampères c’était assez costaud pour bien faire chauffer, mais pas au point d’être dangereux électriquement parlant. J’avais aussi les pinces crocodiles, des chutes de fil électrique, ainsi que la gaine thermique. Pour le reste, direction internet.
Déjà la prise femelle pour raccorder le transformateur au fil chaud, en faisant attention à ce qu’elle soit aux dimensions de la prise mâle de mon adaptateur, j’ai trouvé un lot de 10 faites pour le 12V 3A, parfait. Pour l’interrupteur, comme il s’agissait d’un simple contact on/off je suis parti sur un truc conçu pour le 230V 30A, assez gros et voyant pour éteindre facilement en cas d’urgence. Concernant le potentiomètre j’ai été un peu plus tatillon, je voulais m’offrir le luxe d’un affichage digital, j’ai trouvé ça sans problème, affichage de 0 à 100, résistant à 5A et couvrant de 6 à 30V, superbe !
Niveau budget rien à redire, j’en ai eu pour moins de 15€.
Le passage compliqué (mais pas trop)
Ce qui m’inquiétait le plus dans la préparation de cet outil, c’était de choisir le bon fil de nichrome. Parce qu’il y en a un assez large choix, et chacun a ses performances de chauffe.
Pour ma part je me suis servi d’un petit outil trouvé sur le net : NichromeCalc vous permet de savoir quel type de fil de nichrome vous avez besoin en fonction des critères que vous entrez. Réponse pour mon projet : 32Gauge (ou plus simplement un calibre de 0.2mm).
Le budget ? 3€ le rouleau de 10 mètres.
On passe à l’action
J’ai commencé par choisir une belle planche de 40x40cm en contre-plaqué de 15mm. Pourquoi si épais ? Parce-que je voulais une surface solide, qui ne se déforme pas lorsque je l’utilise. En dessous j’ai prévu une coffret de 30x35cm mesures extérieures réalisé avec des planches de palettes en bon état (mis à part la façade qui recevrait les commandes que j’avais d’abord prévue en plexi). Les planches de palette étant assez épaisses pour faire un support solide, les mesures intérieures de mon caisson sont donc d’environ 26x33cm. Et comme je voulais pouvoir ranger ma potence à l’intérieur de ce caisson, celle-ci ne pouvait donc excéder ces mesures. J’en ai donc fabriqué une de 26cm par 28,5cm avec deux bouts de profilé en alu reliés par une équerre en métal, ce qui s’est assez vite révélé trop fragile et que j’ai donc consolidé avec un triangle en métal qui fait désormais office de bracon.
Pour le fonctionnement la potence serait fixée à l’arrière du plateau, je pouvais donc déjà voir à quel endroit le fil traverserait le plateau. J’y ai fais un trou de 4 mm, agrandit des deux côtés de la planche avec une mèche plus grosse dans le but dy coller une rondelle métallique qui viendrait à fleur du plan de travail. Son rôle est principalement de protéger le bois du fil chauffé.
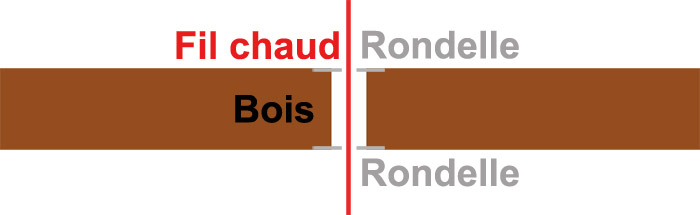
Concernant la fixation de la potence, je souhaitais pouvoir l’incliner, ce qui me permettrait de faire de coupes en biais et non pas seulement en angle à 90°. Pour ce faire j’ai décidé de la fixer par une simple vis, serrée à la main, mais il me fallait un pas de vis femelle assez solide et je doutais qu’un insert à bois supporte les multiples serrages/desserrages qui sont au programme. Je perçais donc l’arrière du caisson là où la vis de fixation (qui servirait aussi d’axe de rotation de la potence) allait le traverser et à l’intérieur du caisson j’ai vissé au bois une petite plaque métallique sur laquelle j’ai soudé un écrou. D’expérience, c’était bien assez solide !
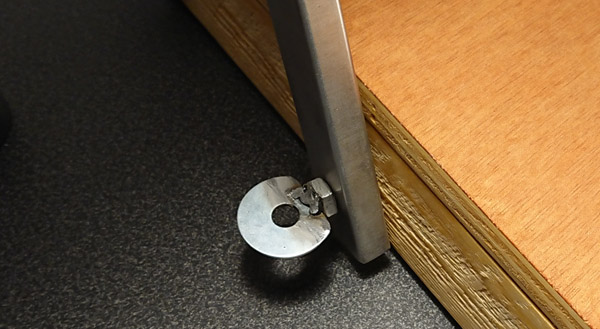
Pour fixer le fil à la potence, j’ai profité du fait qu’elle soit faite avec un profilé et j’ai modélisé en 3D et imprimé une pièce qui viendrait s’insérer en force. Ainsi je pourrais placer le fil selon différents angles avec une relative précision.
Lorsqu’il chauffe, le fil de nichrome se dilate, pour le maintenir tendu une fois chauffé j’ai fabriqué en vitesse un petit ressort avec un fil de soudure en inox.
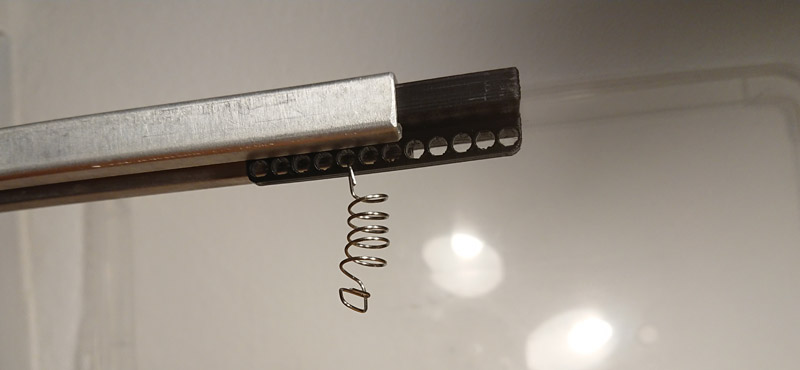
Pour réaliser le panneau avant, celui qui supporterait les commandes, j’optais initialement pour une plaque de plexi, voir de bois, d’une épaisseur de quelques millimètres. Mais je suis par hasard tombé sur une chute de tôle en inox qui, une fois coupée aux bonnes dimensions, fesait une formidable façade. L’inox est un métal particulier à travailler. Percé à grande vitesse il chauffe vite et use le tranchant des forets standards, tout comme les dents des lames de scie. Sans les équipements adaptés il peut devenir une plaie à travailler… Et ça s’est justement révélé fort laborieux pour ma part !
Après avoir tracé les découpes, j’ai percé les coins et fais les découpes à la scie sauteuse, qu’il m’a ensuite fallut ajuster à la lime.
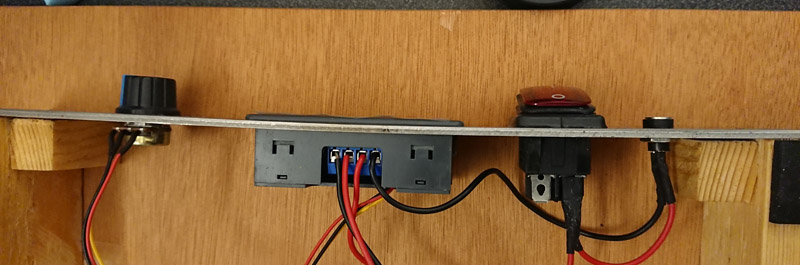
J’ai repris le boitier inférieur et ajouté un carré en bois à chaque coin, il servent à renforcer l’ensemble mais surtout à mettre en appui le fond amovible qui servirait de couvercle. Je découpe d’ailleurs celui-ci dans une plaque de contreplaqué de 6mm qui tient en force dans le cadre du caisson. Ces cales voient la potence prendre appui contre elles lorsqu’elle est rangée à l’intérieur du caisson, pour la fixer j’ai profité de l’écrou soudé installé auparavant.
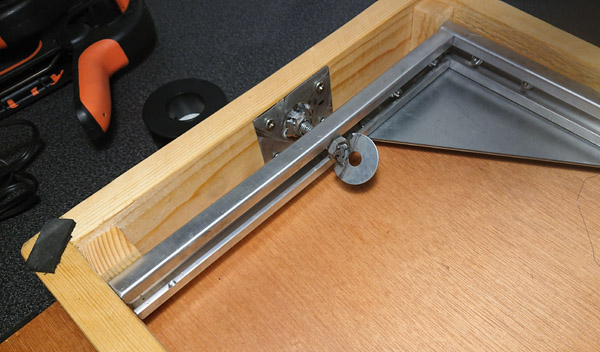
Vinrent ensuite les finitions. Ajout de patins en feutrine pour protéger les surfaces sur lesquelles je pose/range la machine, ajout d’une poignée pour le transport, et, vu qu’il ne contient pas dans le caisson, j’ai installé deux inserts M6 dans le côté extérieur libre pour y fixer un bout de profilé qui servirait de guide pour les découpes droites.
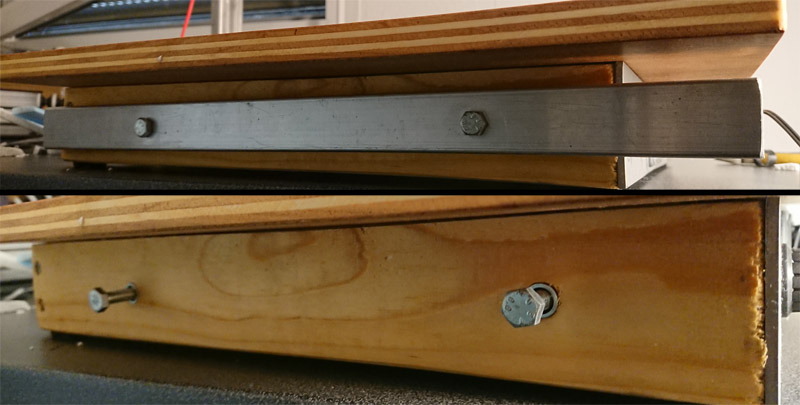
Mise en place et fonctionnement.
Pour mettre en place le fil chaud, c’est très simple. J’ouvre le caisson inférieur qui contient tout le matériel : adaptateur, potence, fil de nichrome (la bobine également pour avoir du rechange), fil de contact, une équerre et des pinces pour maintenir le guide.
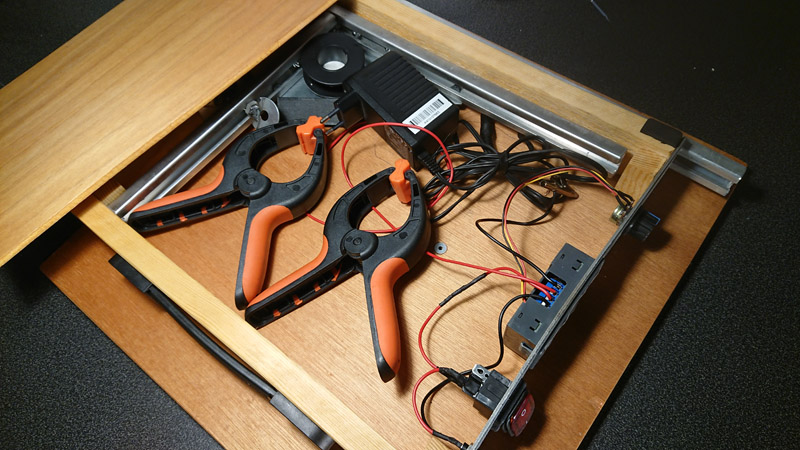
Je passe le bout de mon fil par le trou de la rondelle et le tire jusqu’à ce que la pince enroulée à son extrémité se plaque contre la rondelle. Je remets le plateau dans le bon sens, visse la potence, installe l’embout plastique et son ressort à son extrémité, ce même ressort sur lequel je tire pour y entortiller le bout libre du fil de nichrome qui doit donc être suffisamment tendu. Juste en-dessous du ressort je place une pince crocodile reliée à un fil électrique qui amène le courant. Je n’ai plus qu’à brancher, allumer, et hop, prêt à découper !

Mais avant d’allumer j’ai la possibilité d’utiliser mon équerre pour placer le fil à 90° du plateau en jouant sur l’inclinaison de la potence ainsi que sur l’embout plastique du ressort. De la même manière je pourrais tout à fait régler le fil pour des découpes à un angle de mon choix en utilisant un rapporteur pour le réglage.
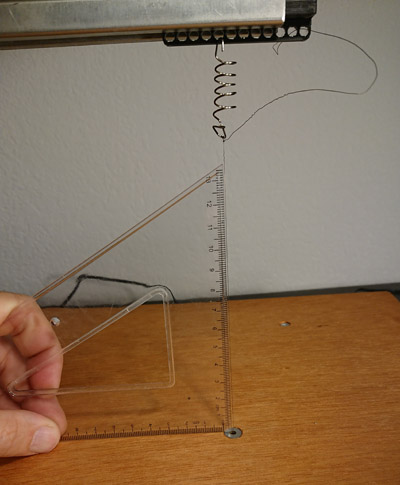
Une fois allumé, monter ou descendre la pince qui amène le courant sur le fil me permet un réglage grossier de la puissance de chauffe, réglage que je peux affiner à l’aide du potentiomètre de façade.
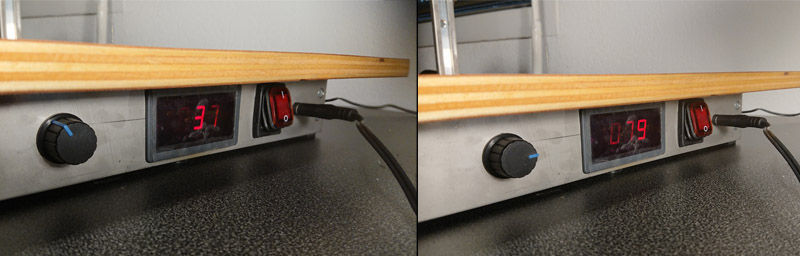
Et c’est parti pour la découpe !
Les problèmes/lacunes (parce qu’il en faut bien)
Globalement je suis super satisfait de ce fil chaud, mais objectivement il y a encore de quoi améliorer/optimiser.
Du côté du fil en lui-même tout d’abord, la manière dont il est maintenu en bas (enroulé autour d’une pince) ne me satisfait pas. C’était une solution temporaire qui est restée telle qu’elle.
La fixation en haut ne me satisfait pas non plus. Actuellement à chaque nouvelle utilisation je dois passer le fil dans l’anneau du ressort puis l’entortiller, ce qui fragilise le fil et lui laisse des marques de plis, de plus, avoir le ressort vertical crée une articulation (au nœud ressort/fil) qui fait que le fil, même bien tendu, prend de l’angle durant la découpe. Enfin, la pièce imprimée en 3D, même si elle rempli très bien son office, rendra l’âme un jour ou l’autre car le peu de chaleur qui lui est transmise la déforme à la longue.

Pourquoi V1 ?
Parce-que je planche sur une V2. Non pas faire un nouveau fil chaud, mais simplement apporter à celui-ci les modifications nécessaires pour corriger ses défauts et améliorer son utilisation. Toute la fixation du haut est à revoir et j’ai déjà mon idée : un système de ressort horizontal avec une poulie, à voir comment bricoler ça et l’adapter à la potence sans perdre trop de hauteur de coupe. Pour la fixation du bas je ne sais pas encore trop comment faire, mais la solution viendra. Le couvercle du caisson lui aussi a besoin d’être amélioré, une fois fermé il est compliqué à ouvrir car ne présente pas de prise, mais il arrive qu’il s’ouvre de lui même et je veux sécuriser ça. J’hésite encore entre placer des aimants ou un vrai système de fermeture… A voir.
En espérant que ce petit article vous donne envie de bricoler vous-mêmes vos propres outils, et pourquoi pas de partager votre retour d’expérience. 🙂
Merci pour cet article très intéressant et c’est clairement le type d’outil qui donne envie d’investir. 🙂